Metal Injection Molding (MIM) has been in production since the 1970s. During that time the market has expanded enormously to include a broad array of applications; the initial successes were in dental orthodontic brackets, watch cases, and firearms, but recently the technology has moved into higher performance, life-critical applications in dental implants, artificial joints, heart pacemakers, and aerospace jet engines. As it has obvious advantage in producing small metal parts that have complex shape, parts that produced by this technology will have high density and strength as well as can be used in molding with one step, it has drawn many attentions. Since then, it has been used in producing various metal material products.
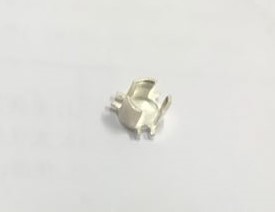
Among them, titanium and titanium alloy is a kind of metal material that has low density, high specific strength, strong corrosion resistance, good creep resistance under high temperature as well as good welding property and biocompatibility, which has been widely used in aerospace and other advanced areas as well as medical treatment, electronic, physical education, leisure and other fields that are closely related with people’s life.
However, as the extracting and smelting of titanium will be much more difficult than the ordinary metals, the production cost will be very high. Besides, by producing titanium and titanium parts with traditional machining methods, it will cause a large amount of material waste as the material utilization is very low. Therefore, it will have high production cost by producing parts with this method, which can be regarded as the main factor that will limit the wide application of titanium and titanium parts.
The emergence of powder metallurgy, especially metal injection molding technology, has provided a possibility of reducing the production cost of titanium and titanium alloy parts. This is because the mixture of powder and specific binder will be used as the injection feeding in this technology, thus it will have high material utilization and will almost not cause any waste. In addition, even if some drainage opening materials will be generated, they will be easy to gather and will be quickly reused in the titanium injection molding manufacturing process.
In fact, it had been put forward by producing titanium and titanium alloy products with injection molding method in the early stage of powder injection molding technology, but it had not achieved large progress until the late of 1980’s. Potable splint was the first kind of metal injection molding product that produced by Japan in 1992. Two years later when BASF SE invented polyacetal resin catalytic debinding technology, many companies began to enter the titanium injection molding field.
However, for a long period of time, most of the companies did not produce any product. This is because powder is very expensive, besides, low-cost titanium powders and titanium alloy powders will have irregular shape and poor sintering performance, which are not suitable for being used in titanium injection molding technology; while the high quality powders that produced by gas atomization or rotate electric method will be very expensive.
At present, with the progress of pure titanium powder and titanium alloy powder preparation methods as well as the improvement of equipment, for example, with the development of hydrogenation dehydrogenation method, gas atomization method as well as powder mixing method and pre alloying method, it will provide technology and equipment foundation for reducing the production cost of high performance titanium and titanium alloy powder as well as will provide a solid backup force for the development of titanium injection molding in the future.