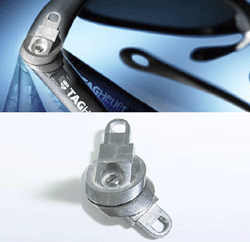
Rotating spring hinge developed for a TAGHeuer spectacle frame.
Metal Injection Molding for watch components
Metal Injection Molding has made great strides in establishing itself as a cost-efficient manufacturing technology for innovative watch designs, ranging from the everyday stainless steel watches to luxury, diamond-clad timepieces.
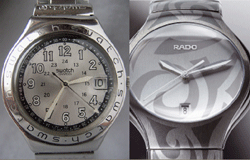
Citizen Watch Co was the first of the watch companies to establish an in-house Metal Injection Molding facility in Tokyo, Japan, in 1987 to produce parts such as stainless steel watch cases and tungsten alloy balance weights used in automatic watches.
Swatch Irony watches were also an early application for stainless steel Metal Injection Molding watch cases. The first Metal Injection Moulded nickel-free 316L stainless steel Irony watch cases for Swatch came off ETA Manufacture Horlogere Suisse’s in-house MIM production line in Grenchen, Switzerland, in October 1994.Citizen Watch Co was the first of the watch companies to establish an in-house Metal Injection Molding facility in Tokyo, Japan, in 1987 to produce parts such as stainless steel watch cases and tungsten alloy balance weights used in automatic watches.
Eyewear components
Spectacle frames have developed into a major segment for Metal Injection Molding because the technology offers previously impossible design options, as well as cost effective high volume manufacturing.
The rotating MIM spring hinge shown in Fig. 32 was an entirely new and revolutionary design that cannot be manufactured economically by other technologies.
The hinge is composed of two rotating discs at an angle of 27° that swivel the spectacle temple with a spring effect. These parts weigh 2.6 g and are made from 316L stainless steel, polished and nickel coated.The rotating MIM spring hinge shown in Fig. 32 was an entirely new and revolutionary design that cannot be manufactured economically by other technologies.
Photographic tripod body
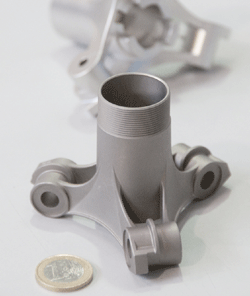
These very large MIM parts, produced in titanium for high-end models and stainless steel for standard models, were manufactured for the leading photographic tripod manufacturer, Lino Manfrotto + Co. SpA, Italy.
The part was machined after sintering to remove supports and create an external thread. Shown in figure in the foreground is the titanium version and, in the background, the stainless steel version.
MIM guitar tuner casing
An automatic tuner for electric guitars was developed and produced by MIM process .
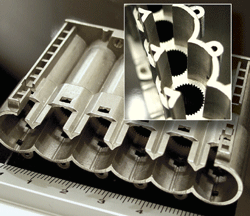
The guitar tuner’s large stainless steel body shows the high level of complexity achievable by MIM as a one-piece part.
Complex shapes can be economically produced by investing only once in a single mould, giving a short ‘pay back’ time.The guitar tuner’s large stainless steel body shows the high level of complexity achievable by MIM as a one-piece part.